In the construction of modern storage facilities, steel structure warehouses have become one of the mainstream building forms due to…
The poultry breeding industry is continually reforming and innovating with the rapid development of agriculture and the economy. The steel structure poultry building is a new type of poultry breeding building. It has the characteristics of fire resistance, water resistance, acid and alkali resistance, corrosion resistance, lightweight, and thermal insulation. The internal structure adopts vertical columns as vertical supports, which increases the space of the poultry building, facilitates the ventilation of the chicken house, and dramatically improves the inside environment of the chicken house. The occurrence probability of the disease is reduced, and the production efficiency is exerted.
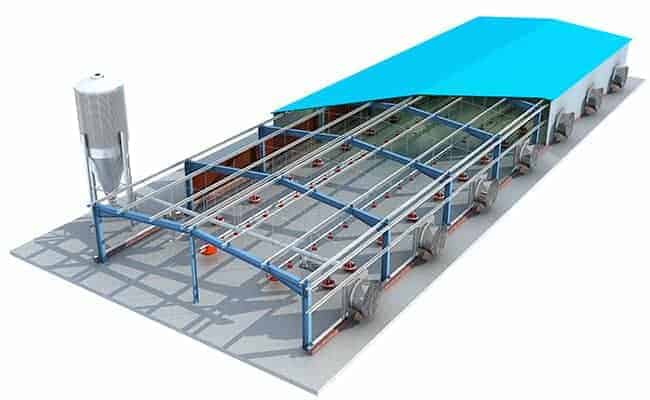
Types of steel structure poultry building:
The steel structure poultry building mainly adopts two kinds of structure: The truss structure and the portal rigid frame structure.

1. The triangular roof truss structure
The truss structure is welded with steel pipes, angle irons, square pipes, C-section steel, etc.

2. Portal rigid frame
The rigid portal frame is a traditional structural system. The upper main frame of this type of structure includes inclined roof beams, steel columns, bracing, purlins, tie rods, wall girt, etc. The steel structure of a portal-type rigid frame lighthouse has the characteristics of pure force receiving, a clear force transmission path, active component manufacturing, convenient factory processing, and short construction time.
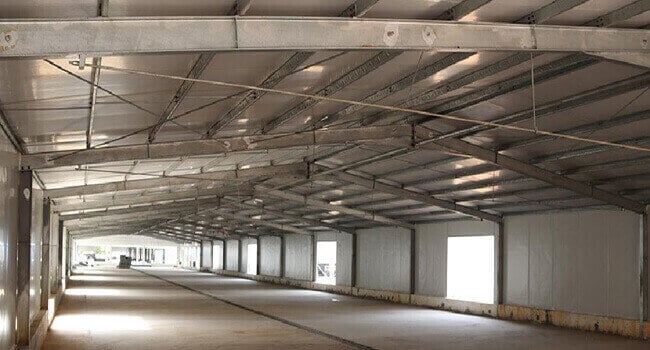
The components of a steel structure poultry building
1. Civil engineering:
Foundations, floors, brick walls, etc.

2. Primary Framing
Steel columns, roof beams, wind-resistant columns.

(1) Steel columns are steel structures’ prominent load-bearing structural members.
(2) Roof beams and steel columns form a load-bearing system.
(3) Wind-resistant columns transfer the loads on the gable roof on both sides to the entire system.

3. Secondary steel structure
Secondary steel mainly includes tie rods, horizontal roof bracing, wall bracing, roof purlin, and wall girt.

4. Roof and wall panels
Corrugated single color sheet, sandwich panel, color steel sheet with insulation cotton
The thickness of the corrugated color sheet is 0.4mm, 0.5mm, 0.6mm
The sandwich panel uses rock wool or polyurethane sandwich panel, and insulation cotton uses glass wool.
Structural requirements for steel structure poultry building
Foundation and Floor: The foundation should be deep and solid. The floor must be higher than outside the house, moisture-proof, flat, and easy to clean and disinfect.
Walls: Good thermal insulation properties and can protect against external wind and rain. They are mostly built with bricks or stones, cement joints on the outside, and cement or white ash inside to prevent moisture and facilitate erosion.
Roof: Double-slope roofs are generally used except for single-slope roofs for tiny chicken houses with small flat spans.
Doors and windows:
Doors are generally located on the south side of the south-facing chicken house. The door size is generally a single door with a height of 2 meters and a width of 1 meter, a double door with a height of 2 meters and a width of about 1.6 meters.
The windows of the steel structure poultry building should be located on the front and rear walls, and the front window should be broad and low to the ground to facilitate lighting. The ratio of windows to ground area is 110 to 18. The rear window should be small, about 2/3 of the front window area, and can be higher from the ground to facilitate ventilation in summer. There are no windows in a closed chicken house, only emergency windows, ventilation inlets, and outlets.
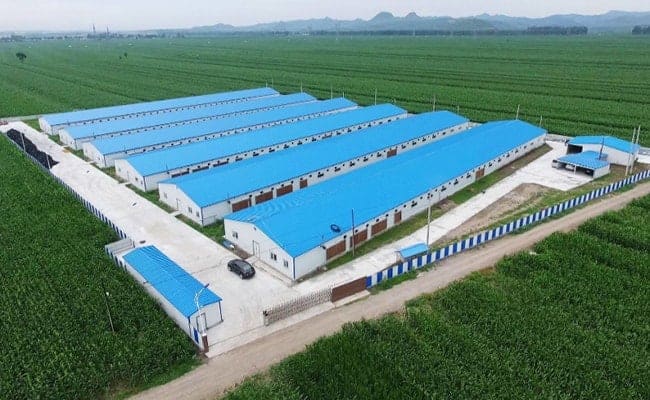
House span, length, and height:
The span of the steel structure poultry building depends on the form of the chicken house roof, the type of chicken house, and the feeding method. The general span is 6 to 10 meters for open chicken houses and 12 to 15 meters for closed chicken houses.
The length of the steel structure poultry building generally depends on the span of the chicken house and the degree of mechanization of management. Chicken houses with a span of 6 to 10 meters are usually 30 to 60 meters long; chicken houses with a larger span, such as 12 meters, are generally 70 to 80 meters long.
Chicken houses with a higher degree of mechanization can be longer, but generally, they should not exceed 100 meters. Otherwise, the production and installation of mechanical equipment will be more complex, and the materials will not be easy to deal with.
The height of the steel structure poultry building should be determined according to the feeding method, manure cleaning method, span, and climatic conditions. The chicken house does not need to be too high in areas with small spans, dry farming, and not-too-hot regions.
Generally, the eaves height of the steel structure chicken house is 2.0 to 2.5 meters; if the span is large and it is a multi-layer cage, the chicken house is about 3 meters or more. The uppermost chicken coop is preferably 1 to 1.5 meters away from the roof; if it is a high-bed closed chicken coop, the height is generally 4.5 to 5 meters (1.8 to 2 meters higher than ordinary chicken coops) due to the manure pit at the bottom.
Operation room and aisle:
The operation room is where the breeder performs operations and stores tools. If the length of the steel chicken house does not exceed 40 meters, the operation room can be located at one end of the chicken house. If the size of the chicken house exceeds 40 meters, it should be found in the center of the chicken house.
The location of the walkway depends on the span of the chicken house. The span of a flat chicken house is relatively small, and the walkway is generally located on one side of the chicken house, with a width of 1 to 1.2 meters.
When the span is greater than 9 meters, the walkway is located in the middle, with a width of 1.5 to 1.2 meters—1.8 meters, convenient for feeding by trolley. No matter how large the span of the cage chicken house is, it depends on the arrangement of the chicken cages. The walkway between the chicken cages is 0.8 to 1.0 meters.
Sports ground: When open chicken houses are raised on flat ground, there is usually a sports ground. The sports field is the same length as the chicken house, and the width is about twice the span of the chicken house.
Chicken-raising equipment and utensils
1. Chicken cage is the leading equipment of cage chicken house.
Chick cages
Chick cages are used to raise chicks, generally using 3 to 4 layers of overlapping cells. The total height of the pen is about 1.7 meters, the size of the cage frame is 10-15 cm, the length of each single cage is 70-100 cm, the cage height is 30-40 cm, and the cage depth is 40-50 cm.
The mesh is generally rectangular or square, with the aperture of the bottom mesh being 1.25cm x 1.25cm and the apertures of the side mesh and top mesh being 2.5X2.5cm. The cage door is located in the front, and the cage door gap can be adjusted within a range of 2 to 3 centimeters. Each cage can hold about 30 chicks.
Breeding chicken cages
The combination form is mostly three-layer overlapping, with an overall width of 1.6 to 1.7 meters and a height of 1.7 to 1.8 meters. The single cage is 80 cm long, 40 cm high, and 42 cm deep. The mesh at the bottom of the cell is 4 cm × 2 cm, and the remaining mesh holes are 2.5 cm × 2.5 cm. The cage door size is 14 cm x 15 cm, and each cage can accommodate 7 to 15 adult chickens.
Layer cages
Common combinations include stepped, semi-stepped, and overlapping types. Each pen is 40 cm long, 45 cm deep, 45 cm high in front, and 38 cm tall in the back. The slope of the cage bottom is 6° to 8°. The egg collection trough extending from the cage is 12 to 16 cm.
The cage door opens in front, with a width of 21 to 24 cm and a height of 40 cm. There is a gap of about 4.5 cm between the lower edge and the bottom net: the cage bottom mesh has a hole spacing of 2.2 cm and a weft spacing of 6 cm. The aperture range of the top, side, and back nets varies greatly. Generally, the warp distance of the mesh holes is 10 to 20 cm, and the weft distance is 2.5 to 3 cm. Each single cage can raise 3 to 4 chickens.
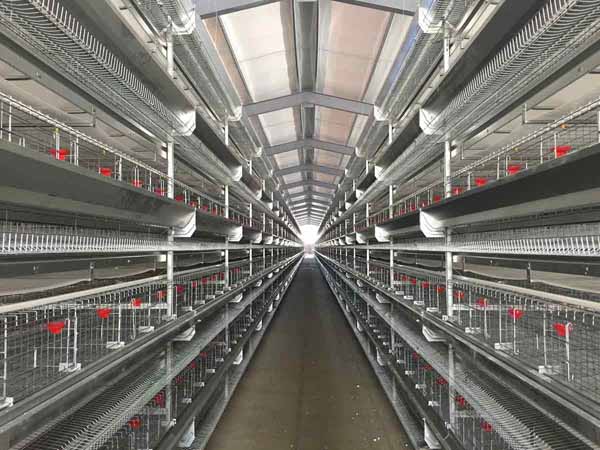
2. Feeding equipment includes feeding machinery and food troughs.
The feeding system of large-scale chicken farms is mechanized, and the feeding machines are equipped with troughs.
Chain feeder system: It is the most commonly used feeder in my country’s feeding machinery. It can be used for both flat and caged feeding. It consists of a feed box, a chain link, a driver, a corner wheel, a long trough, etc. Some are also equipped with a feed cleaner.
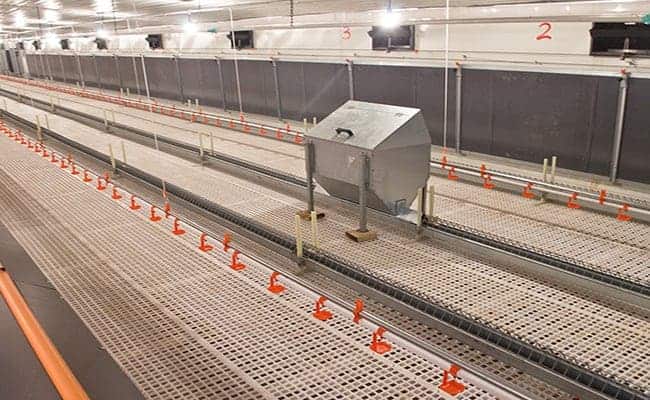
Pan feeding system: It is designed for poultry farming and is suitable for conveying dry powder feed. Pan feeding systems use a series of rotating feed pans, usually made of plastic, to feed at regular intervals within the chicken farm. A motor usually drives these trays and can be automatically timed or rotated to distribute feed to the chickens’ feeding areas.
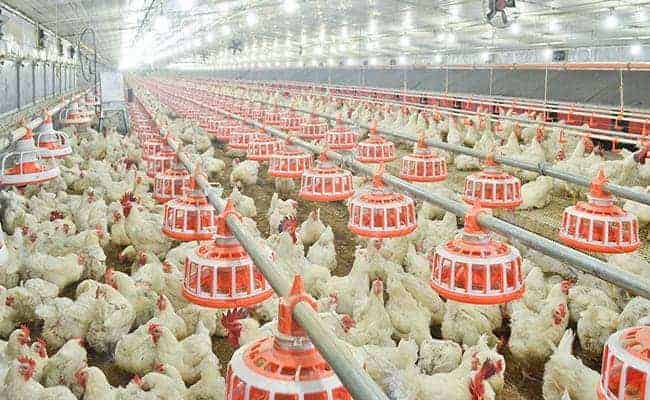
Food troughs: Common ones include long and bucket-type round food troughs.
Drinking water equipment
Long sink: Its advantages are simple structure, low cost, convenient drinking water, and immunity. The disadvantages are that it consumes a lot of water, is susceptible to contamination, and requires much scrubbing work.
Vacuum drinking fountain: Its advantages are a balanced water supply and ease of use. The disadvantage is that the cleaning workload is large and cannot be used when drinking large amounts of water.
Nipple drinking fountain: Its advantage is that it saves water, is conducive to epidemic prevention, and does not require frequent cleaning and replacement. The disadvantage is that each layer of chicken cages needs to be equipped with a decompression water tank, which is not conducive to drinking water immunity, and the material and manufacturing accuracy requirements are also high.
Cup-type drinking fountain: Its advantage is that it can supply water according to needs and save water. The disadvantage is that the water cup needs to be cleaned frequently and equipped with a filter and a water pressure adjustment device.
Suspended plate drinking fountain: The advantages are water saving and easy cleaning. The disadvantage is that the height of the waterer needs to be adjusted according to the different growth stages of the chickens.
Ventilation and cooling equipment for Steel Structure Poultry Building
Chicken house fan:
The fan is installed on the wall of the steel structure poultry building. The ventilation and cooling effect of the fan has a great relationship with the fan model, installation method, and usage method used. The appropriate ventilation method should be selected based on the construction of the chicken house.
Generally speaking, Longitudinal ventilation along the chicken house has a better effect. The technique is simple, economical, and practical.
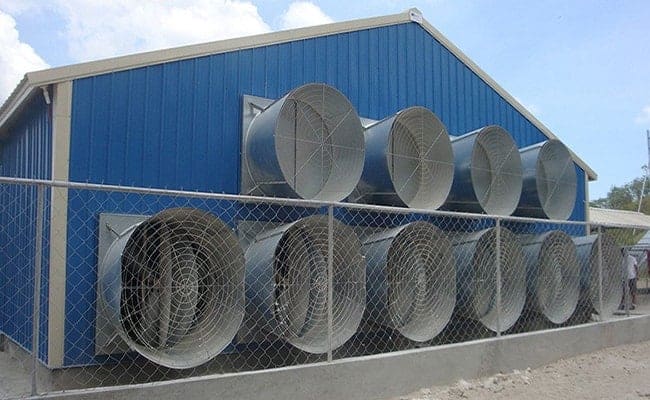
Wet curtain-fan cooling equipment:
The equipment is a new type of cooling equipment, mainly composed of two parts: a wet curtain and a fan.
A solid negative pressure flow is formed in the steel structure poultry building through the longitudinal ventilation of low-pressure and large-flow energy-saving fans. The hot air outside the home is cooled through the wet curtain and enters the chicken house, thereby reducing the temperature of the chicken house.
This wet curtain fan cooling equipment has a remarkable effect and is suitable for closed or semi-open chicken houses.
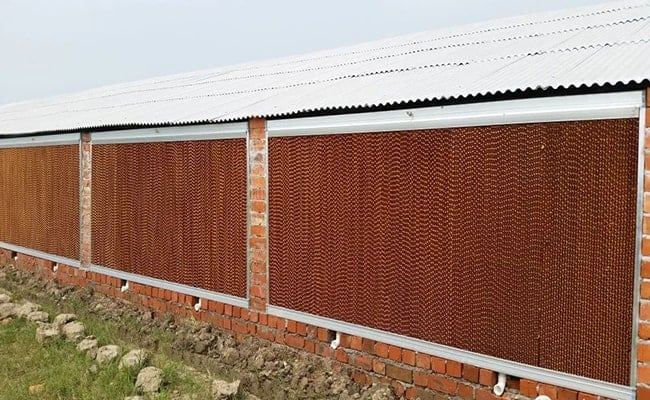
Automatic spray cooling equipment:
It mainly consists of a water tank, pump, filter, nozzle water pipe, and automatic control system. In addition to spraying water for cooling, the automated spray equipment can add a certain proportion of disinfectants to the water to prepare a corresponding liquid concentration to spray and disinfect the chicken house or the chickens. This can prevent heatstroke and cool down, and Disinfection and sterilization.
Design principles for steel structure poultry building:
1. According to the production process requirements of different livestock and poultry farms, combined with local conditions, topography, and surrounding environmental characteristics, the functional areas should be divided according to local conditions. Reasonably lay out various buildings to meet their functions and create a reasonable production environment.
2. Make full use of the site’s original natural topography and topography, arrange the long axis of the steel structure poultry building as much as possible along the site’s contour lines, minimize the amount of earthwork and infrastructure engineering costs, and minimize infrastructure construction costs.
3. Reasonably organize the flow of people and logistics inside and outside the site, create the most favorable environmental conditions and low labor intensity production connections, and achieve efficient production.
4. Ensure that the building has a good orientation, meets lighting and natural ventilation conditions, and has sufficient fire separation distance.
5. Facilitate treating and utilizing feces, sewage, and other wastes to ensure they meet clean production requirements.
6. Under the premise of meeting production requirements, the building layout is compact, saving land and occupying little or no cultivated land. While occupying an area that meets current functions, future development should be fully considered and leave room for growth.