A steel portal frame structure is a type of low-rise building composed of steel columns and rafters joined by rigid…
Steel warehouse building design is not simply a matter of assembling prefabricated components—it’s a discipline that blends structural engineering, environmental adaptation, and functional planning. A well-designed steel warehouse addresses both the technical demands of load-bearing stability and the practical considerations of cost, durability, and usability. This article presents a detailed case study of a 2,000-square-meter prefab steel warehouse in Tanzania, offering insights into the design process, structural calculations, and the broader implications of modern prefabricated steel construction.
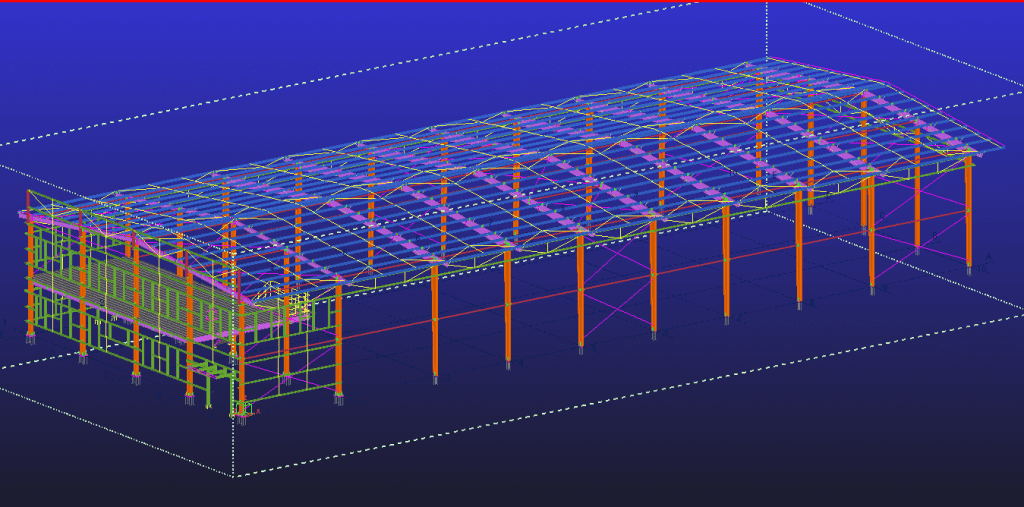
Steel Warehouse Building Design: The Role of Drawings
In steel warehouse building Design, design drawings serve as both the conceptual and operational foundation of the project. They are generally divided into two essential categories: structural drawings and construction drawings.
Structural drawings articulate the skeletal framework of the building, specifying dimensions, material grades, member sections, and connection types. These drawings are crucial for translating design intent into quantifiable engineering standards.
By contrast, construction drawings function as implementation guides for site teams. They detail the sequence and method for assembling prefabricated components—from foundation bolts and anchor plates to roofing systems—ensuring consistency and accuracy during on-site erection.
The quality of these drawings directly impacts project efficiency, safety compliance, and construction timelines. They are not simply design documents, but operational blueprints that ensure a smooth transition from theory to execution. smooth construction flow, help prevent errors, and directly influence the final build quality and timeline.
Engineering for Stability and Cost Efficiency
The structural soundness of a steel structure warehouse rests primarily on its frame, typically composed of H-section steel columns, beams, and connections. Undersized sections risk structural failure under wind, seismic, or snow loads. Oversizing, however, leads to inefficient use of steel and inflated costs.
Therefore, during steel warehouse building design, structural engineers conduct thorough analyses based on site-specific parameters—such as wind pressure, seismic intensity, and live load requirements—to calibrate member sizing. The objective is dual: to ensure structural integrity while minimizing material consumption, thereby enhancing both safety and cost-efficiency.
Steel Warehouse Building Design in Tanzania
Havit Steel Structure was contracted to design and fabricate a steel warehouse facility tailored to local climatic and operational requirements. The completed structure spans 2,000 square meters, demonstrating how prefabricated steel systems can be flexibly applied to real-world conditions.
Project Specifications:
- Length: 100 meters
- Width: 20 meters
- Eave Height: 7.7 meters
- Additional Feature: 4.5-meter-high front mezzanine for office use
- Design Software: PKPM (structural analysis)
This project integrates warehouse and office functions into a single unified structure, maximizing spatial utilization while adhering to regional load standards.
Read more: Feed Mill Steel Building In Tanzania
Steel Warehouse Building Design: Structural Loads and Engineering Parameters
Load Type | Value |
---|---|
Dead Load | 0.3 kN/m² |
Live Load | 0.5 kN/m² |
Wind Load | 0.6 kN/m² |
Snow Load | Not Applicable |
Seismic Design | 7 degrees, 0.1g |
Brick Wall Height | 5 meters |
These values reflect localized environmental loads in Tanzania and serve as the basis for structural calculation and detailing.
Key Components and Connection Details
Steel Frame System
- Steel Grade: Q345B
- Main Frame: Welded H-section columns and beams
- Beam-Column Connection: High-strength bolts
- Foundation Anchors: M20×900 anchor bolts, 4 per column
Secondary Framing and Enclosures
Wall Cladding: 0.5mm pre-painted metal sheeting
Roof & Wall Bracing: Round steel
Tie Rods: Welded pipe
Purlins & Girts: Galvanized C-section, spaced at 1.5 meters
Sag Rods: Round steel
Roof Panels: 50mm polyurethane sandwich board
These components combine to create a robust, modular frame capable of withstanding regional environmental loads while allowing efficient prefabrication and transport.
Read more: steel structure components
Advantages of Prefabricated Steel Structure Buildings
1. Broad Functional Flexibility
Steel buildings are well-suited for a range of applications—from warehouses and factories to hangars, stadiums, and commercial centers. Their clear-span design is particularly beneficial for unobstructed internal layouts.
2. Rapid Deployment
Because components are manufactured in a controlled factory setting, on-site assembly is streamlined and significantly faster than traditional construction. This results in shorter project cycles and reduced labor overhead.
3. Durability and Minimal Upkeep
Steel buildings offer high resistance to environmental wear and require little maintenance over their service life. Proper corrosion protection and detailing ensure longevity even in coastal or humid climates.
4. Cost-Efficiency Across the Lifecycle
Although initial material costs may be higher than concrete, the long-term savings from reduced labor, faster installation, and energy efficiency make prefabricated steel buildings a financially viable solution.
Conclusion: A Smart Investment for Growing Industrial Needs
The Tanzania steel warehouse building design exemplifies how prefabricated steel buildings can be tailored to local needs while ensuring performance, speed, and economy. Through careful structural planning and modern fabrication technologies, steel structures offer a compelling alternative to traditional methods.
For businesses requiring logistics, storage, or multipurpose facilities, investing in steel construction offers both immediate practicality and long-term value.
FAQs about Steel Warehouse Building Design
What are the essential components of a steel warehouse building?
A typical steel warehouse includes welded H-beam frames, galvanized purlins and girts, bracing systems, anchor bolts, and insulated roofing and wall panels.
How long does it take to complete a steel warehouse project?
Construction time varies by scale, but most prefabricated steel warehouses can be erected within a few weeks due to the high degree of factory preassembly.
What factors influence the cost of a steel warehouse?
Costs depend on design complexity, steel quantity, insulation type, environmental loads, and logistics. Optimizing these factors through good design helps control budget while maintaining safety.
Can steel warehouses withstand strong winds or earthquakes?
Yes. When designed according to local load codes, steel buildings offer excellent structural performance under seismic or cyclonic conditions.
Is it possible to integrate office space into a warehouse?
Certainly, mezzanine levels or modular office sections can be incorporated into the building plan, enhancing functionality without major cost implications.
What are the long-term benefits of prefabricated steel structures?
They combine fast construction, material efficiency, structural resilience, and design flexibility—ideal for businesses seeking sustainable and scalable infrastructure.
Call to Action
If you’re seeking a reliable steel warehouse building design, this project demonstrates a high-performing model tailored to local environments.? Havit Steel Structure provides full-service solutions—from structural design and fabrication to delivery and installation support. Contact our expert team today to get a tailored quote and design proposal for your project.