Steel Garage Building
In an era where efficiency, longevity, and cost-effectiveness define the benchmarks of construction, steel garage buildings have emerged as a compelling solution for a wide array of storage and workspace requirements. No longer limited to basic vehicle shelters, these structures now serve a diverse range of residential, commercial, and industrial purposes. Their growing popularity is rooted in a combination of structural resilience, design versatility, and economic viability.
This article critically examines the practical advantages of steel garage buildings, highlights their design attributes and customization potential, and explains why they represent a sustainable investment for modern users.
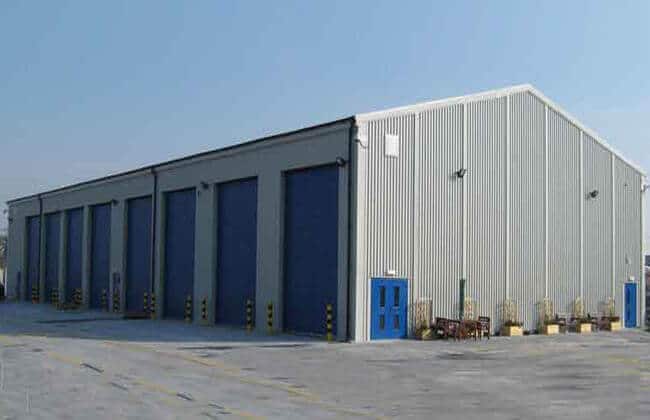
Description of Steel Garage Building
Why a Steel Garage Building Is the Smart Choice for Modern Storage
The transition from traditional materials to steel in garage construction is not merely a trend but a reflection of informed decision-making grounded in long-term value.
1. Structural Integrity and Lifespan
Steel exhibits exceptional resistance to decay, termites, moisture, and fire—hazards that often compromise wood or masonry structures. With minimal maintenance, a professionally installed steel garage building can easily maintain its structural integrity for several decades, often exceeding 40 to 50 years.
2. Economic Efficiency
Prefabricated steel garage kits significantly reduce construction timelines and associated labor costs. Unlike conventional builds, where on-site fabrication can inflate expenses, steel buildings arrive ready for rapid assembly, often within a few days.
3. Minimal Maintenance Requirements
Galvanized or coated steel panels resist corrosion and require little more than occasional cleaning. There is no need for repainting, termite treatments, or frequent structural inspections, which translates to long-term savings and peace of mind.
4. Enhanced Safety and Security
The inherent strength-to-weight ratio of steel provides high load-bearing capacity while offering excellent performance against seismic events, snow loads, and high winds. These attributes are particularly valuable when storing high-value equipment or sensitive materials.
5. Sustainability and Environmental Performance
Steel is not only recyclable but often composed of recycled content. By opting for steel construction, users contribute to a reduction in deforestation and carbon-intensive practices—aligning their projects with modern sustainability benchmarks.
Application
Functional Versatility: Applications of Steel Garage Buildings
A key reason for the widespread adoption of steel garage buildings lies in their functional diversity:
-
Private Vehicle Storage: Offering year-round protection for cars, motorcycles, and RVs.
-
Workshops and Studios: Ideal for tradespeople or hobbyists needing a dedicated and insulated workspace.
-
Commercial Storage: Suitable for storing service vehicles, construction tools, or inventory materials.
-
Agricultural Utility: Used for housing tractors, machinery, and feed supplies in rural settings.
-
Home-Based Enterprises: Can be tailored into multi-functional spaces, such as repair shops or small-scale production facilities.
Steel Garage Design
Core Design Features of a Steel Garage Building
Understanding the architectural and structural components of steel garages helps buyers make informed decisions regarding functionality and customization:
1. Framing System
Most steel garages utilize a rigid or portal frame system, characterized by wide clear-span interiors and high load resistance. This open design maximizes usable space and simplifies future layout changes.
2. Cladding and Roofing
Corrugated or ribbed galvanized panels provide superior protection against the elements. Optional insulation layers further enhance thermal performance and noise reduction.
3. Thermal Insulation
For year-round usage, insulation options such as fiberglass blankets, polyurethane panels, or spray foam are commonly integrated. These materials improve comfort while lowering energy consumption.
4. Access Points
Roll-up garage doors, personnel doors, and ventilation windows are standard features. Their layout can be customized to suit vehicle access patterns, lighting requirements, and airflow needs.
5. Foundation Options
Depending on local regulations and soil conditions, steel garages can be anchored to slab-on-grade foundations, concrete piers, or even temporary base plates for mobile units.
Personalization and Scalability: Adapting Steel Garages to User Needs
Steel garage buildings are inherently modular, allowing for a high degree of customization:
-
Dimensional Flexibility: Available in widths ranging from single-car units to expansive multi-bay structures exceeding 50 feet.
-
Color and Aesthetics: Clients can choose from a range of factory-coated panels in custom color schemes to complement adjacent buildings.
-
Interior Partitioning: Mezzanine floors, dividing walls, and office enclosures can be seamlessly integrated.
-
System Upgrades: Skylights, solar panels, security systems, and drainage components can be added post-installation.
Steel Garage vs. Traditional Garage: A Comparative Overview
Criteria | Steel Garage Building | Wood or Masonry Garage |
---|---|---|
Build Time | Rapid (prefabricated) | Lengthy (on-site fabrication) |
Cost | Lower overall cost | Higher labor and material costs |
Durability | 40–50+ years | 15–30 years |
Maintenance | Minimal | Frequent upkeep required |
Design Flexibility | High | Moderate to low |
Construction Process and Timeframe
Installing a steel garage typically involves the following phases:
-
Site Preparation (1–3 days) – Includes leveling, grading, and foundation setup.
-
Delivery and Inspection (5–14 days) – Prefabricated parts are shipped for onsite assembly.
-
Erection and Finishing (3–7 days) – The structure is assembled using bolted connections, and optional features are installed.
Commercial-scale projects with additional mechanical systems may extend beyond these timeframes.
FAQs about Steel Garage Buildings
Q1: What is the price range for a steel garage building?
The cost varies based on size, insulation, and location. On average, expect prices between $30–$70 per square foot. A basic one-car steel garage may start from $5,000, while larger commercial units can exceed $25,000.
Q2: Can I install the garage myself?
Many manufacturers offer DIY-friendly kits with pre-drilled components and clear assembly manuals. For larger or more complex buildings, professional installation is advisable to ensure compliance with local codes.
Q3: Is a steel garage suitable for extreme weather?
Yes. When properly designed and anchored, steel garages perform well in heavy snow, wind, or seismic zones. Weather-resistant coatings and reinforced framing enhance protection.
Q4: Can I expand the garage in the future?
Absolutely. Steel structures are modular, meaning they can be extended or reconfigured without compromising the original design integrity.
Q5: Do I need a permit to build a steel garage?
Most jurisdictions require building permits for permanent structures. Always consult with your local planning department before beginning construction.
Conclusion: Investing in a Steel Garage Building
A steel garage building is more than a storage solution—it is a long-term asset that offers security, adaptability, and strong return on investment. Its durability, design flexibility, and low life-cycle cost make it an ideal choice for property owners seeking functionality without sacrificing aesthetics or performance.
As construction preferences shift toward more sustainable and efficient methods, the steel garage continues to stand out as a future-ready building choice across residential and industrial landscapes.